The first yarn upcycling mill from textile waste is now open for business in Hong Kong and ready to share its yarn with the world!
We got the opportunity to visit the first yarn processing mill that has opened in Hong Kong in almost half a century. But that’s not all that’s exciting. This is not your ‘run of the mill’ mill; they are truly committed to bringing a solution to Hong Kong’s 300 tonnes-per-day textile waste problem and offering a solution to global manufacturers and retailers alike.
The brand-new mill came to fruition with a partnership formed between HKRITA (The Hong Kong Research Institute of Textiles and Apparel) and Novetex (a leading textile firm), together with funding from HKSAR government, H&M foundation and The Mills. During our visit, we were given a tour of the factory in Tai Po by Mr. Max Ng, their production control director. The factory can currently upcycle up to 1 ton of textile waste per day; they’ll be adding another two lines by the end of March, and will then be able to re-spin up to 3 tons of upcycled yarn per day.
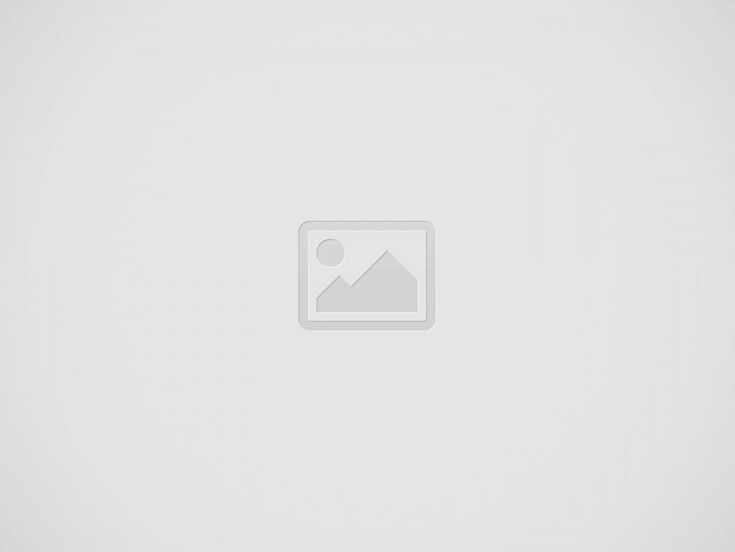
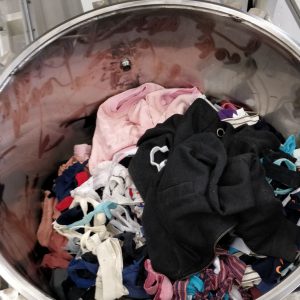
How does it work?
There are two processes on the factory floor: Chemical and Mechanical. Textile recycling and upcycling is not a new thing, and there are numerous yarn recycling and upcycling plants all around the world. However, what sets this one apart and makes it super special, is that HKRITA and Novetex have discovered through their mechanical process how to upcycle virtually any used textile and spin them into slivers WITHOUT using ANY water.
Say what! How is it waterless?
For the waterless mechanical process, textiles from donated boxes get cleaned with O³ (Ozone / Trioxygen) compression, and the offset is turned back into O² so only the good stuff is released back into the air. After cleaning, they get sent via conveyor to the trimming area, at which buttons, zips, and other non-textile components are removed. Then, they get colour sorted by a machine that takes frequency images and automatically separates the groups into different colours. Finally, once they have been sorted by colour (and composition), they get chopped up and extracted back into fibre form, and spun into slivers, which get spun into yarns. The yarns then get sent to the Novetex plant in China where the yarns are turned into fabric and the fabric into garments.
The other process that is super exciting, but still in the testing phase, is the hydrothermal separation of synthetic and natural cellulosic fibres (i.e. Cotton). This is some serious experimentation, as there currently aren’t any commercially scalable solutions to separate blended fabrics back into fibre form. But not to worry, Novetex has come to the rescue! They can now successfully separate the different fibres and harness 100% polyester, which are ready to be re-spun into new yarns.
The tricky part is that the cellulosic fibres come out in powder form, unable to be spun back into yarn. They are currently working with the University of Japan to solve this issue by possibly mimicking the process used to make Viscose by reconstituting the cellulose fibre after making it into a pulp (this one’s for the scientists).
Sharing to save the world.
Their technology is open-source, and the team wants to share with everybody around the globe – sharing is caring, after all! At their mechanical yarn mill in Tsuen Wan, they have an example of how the entire mechanical upcycling system can fit into a 40-foot container. Best of all – they will sell your company this 40ft container. So, there isn’t really a reason why every yarn processing mill should not be fitted with at least one of these lines on factory floors.
Money’s too tight to mention?
Of course, the question arises – how much does this cost compared to buying virgin fabrics? Fact is, recycled yarns are the same price or even cheaper than buying virgin fibre fabrics, as there is little to no new fibres being purchased. For example, upcycled Cotton costs 5% less than virgin Cotton*, whereas Polyster and Nylon will cost the same as virgin materials. Upcycled animal fibre fabrics such as Wool or Alpaca can accrue savings of between 10-15% the cost of virgin material. Novetex can also spin slivers according to customer requirements for fibre contents.
How can I help?
Don’t worry if you don’t work in the fashion industry- you can definitely still contribute to saving the Earth! Here’s #LittleGreenSteps you can take today:
> Ensure that you dispose of old clothing and textiles in a responsible manner. Donate them to NGOs such as the Salvation Army or Redress or check out H&M and Zara – they have used clothing collection points. These companies will sort through the used clothing, and those items that are unfit for redistribution be sent to upcycling or recycling plants such as Novetex.
> There are even textile waste collection bins in and around the city – so recycling your old clothes is as easy as sorting your trash!
And if you’re doing good on your textile waste, why not check out how you can reduce your travel waste today?
*Cost saving estimation – prices are dependent on where the virgin Cotton is produced, as fabric prices vary depending from supplier to supplier / country to country.